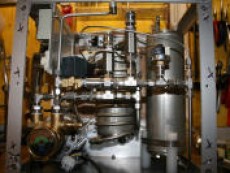
Einer unserer Kunden hat seine Vision in die Tat umgestzt und sich seine eigene Espressomaschine gebaut.
Wir haben dieses Projekt sehr gerne mit Rat und Teilen versorgt und freuen uns hier die Maschine vorstellen zu dürfen. Eine Top-Arbeit bei der nur hochwertigste Materialien eingesetzt wurden.
Sogar eine passende Mühle wurde adaptiert.
Und,……es gibt eine Modellvariante.
Wir sind gespannt auf die Erläuterungen des „Entwickler´s“………..
………….. Der/Die Entwickler, vieleicht ein wenig viel des Guten 😉 trotzdem Danke !
Erst einmal muß ich mich für den Support hier bedanken, ohne den die ganze Geschichte deutlich schwieriger und langwieriger geworden wäre. DANKE !!! Die Maschinen sind zeitgleich von mir und meinem Freund gebaut worden. Nach der gemeinsamen Planung und Teilebeschaffung ist die Umsetzung in getrennten Werkstätten erfolgt. Die beiden Maschinen unterscheiden sich technisch eigentlich nur durch die Espressokesselgröße. Die Basis der Maschinen ist ansonsten vollkommen identisch. Die Ergebnisse, im Bezug auf die Optik, dafür um so verschiedener. Zum Anfang vieleicht ganz nüchtern die Eckdaten:
– Maschinentyp: Dualboilerprinzip
– Brühgruppe: Faema E61
– Pumpe: Rotationspumpe (Messingkopf / Edlelstahl Innenleben) innerhalb der Maschine
– Vorwärmer für Wasserzufluss espressoseitig (Edelstahl)
– Kesselvolumina Espresso: 700 ml/800ml
– Kesselvolumen Dampf: 1200 ml Kesselvolumen mit je 1350 W Heizleistung
– Temperaturregelung Espresso: PID-Regler mit Pt100 + Bimetallabsicherung
– Temperaturregelung Dampf: Pressostat + Bimetallabsicherung
– Alle Rohrleitungen, die Kessel, Ventile… aus Edelstahl (Ausnahmen bilden der Pressostat, ein Magnetventil, der Pumpenkopf und die Heizschlange)
– No-Burn Dampflanze aus Edelstahl, sowohl inneres als auch äußeres Rohr
– Festwasseranschluss mit einstellbarem Druck und Härtegrad (ausserhalb der Maschine)
– Kesselisolierung: vergleichbares Konkurrenzprodukt v. Armaflex
– Gehäuserahmen: Maschine 1 Aluminium Winkelprofile / Maschine 2 Edelstahlrohr
– Gehäusefront und Deckel: Maschine 1 Kupfer / Maschine 2 Edelstahl
– Holzteile: Mahagoni geölt, massiv
– Abtropfgitter: Edelstahl
– Standhaltung Dampfkessel: Maschine 1 manuell per Magnetventil + Schauglas / Maschine 2 manuell + Schauglas
– Mühle: gestrippte Aristarco EMA80 mit Gehäuse aus Mahagoni + Kupfer, Bohnenbehälter aus Glas, Auswurf aus Edelstahl, Wahlweise Dosierung manuell oder per Timer
Das Ziel war, eine robuste, wartungsfreundliche Maschine zu bauen, ohne auf einem niedrigeren Niveau, als die industriell gefertigte Gegenstücke genießen zu können. Ob nun die E61 die optimale Gruppe, Edelstahl oder Kupfer der ideale Werkstoff oder Detaillösungen wie z.Bsp. Wasservorwärmer einen gravierenden Unterschied ausmachen, kann man abendfüllend diskutieren bzw. müßte man aufwändig beweisen. Von der Optik ganz zu schweigen. Und natürlich würde ich heute einiges anders angehen oder Details ändern. Vom Grundkozept her (und das ist ja wahrlich nicht neu) wäre es beim nächsten Mal aber wieder die gleiche Maschine. Der Espresso schmeckt halt 😉
Die Warums:
Maschinenprinzipauswahl:
Für mich hätte es ein Einkreiser mit PID getan, weil ich nur Espresso ziehe. Da kommt dann meine Regierung mit Latte ins Spiel 😉
Zweikreiser empfand ich persönlich zu unstabil, was das Ergebnis angeht. Zu viele Einflussgrößen die die Temperatur beinflussen können. Außerdem ist der Bau eines Zweikreiserkessels zumindest bei meiner Materialwahl etwas schwieriger (Thema Schweißverzug, Materialspannung…) Also Dualboiler.
Den Espressokessel wollte ich so klein wie möglich halten (es ginge noch kleiner) um die Wasserverweilzeit zu verkürzen (ein echter Vorteil der Zweikreiser). Der Nachteil einer kleinen Wassermenge ist die Temperaturstabilität beim Bezug. Kann man kompensieren durch mehr Metall am Kessel oder das Vorwärmen des zulaufenden Frischwassers.
Hier der Vorwärmer.
Nachteile sind der hohe Preis des Edelstahlrohrs bzw. der Verschraubungen und es ist eine sch… Arbeit den richtigen Durchmesser zu wickeln (soll ja schön am Kessel anliegen und Abstrahlwärme nutzen) und noch viel besch. das Ganze dann noch platzsparend anzuschließen. So nicht mehr.
Gruppenwahl:
Die Faema E61, weil sie ausgereift bzw. ihre Schwachpunkte bekannt sind. Das macht die Fehlersuche im Gesamtsystem einfacher als mit einer weiteren Unbekannten, sprich einer weniger verbreiteten Gruppe. Zusätzlich ist sie gut verfügbar, bezahlbar und man bekommt problemlos alle Ersatzteile.
Die Gruppe ist klassisch mit dem Thermosyphon verrohrt. Ich denke aber, das wg. der kleinen Querschnitte in der Gruppe am Kesselaustritt -> Gruppe / Gruppe -> Kesseleintritt nicht wirklich viel zirkuliert. Man erreicht wahrscheinlich mehr durch ein gute Isolierung, kurze Zuleitungen und größere Querschnitte in der Gruppe. Hat jemand eine alte Schrottgruppe die nicht zu retten ist ? Ich zahle den Materialwert und mach dann ein Schnittmodell daraus. Dann kann man daran mal Aufbohrmöglichkeiten diskutieren. Angebot steht.
Ich will aber in jedem Fall noch mal eine federbelastete Handhebelgruppe verbauen.
Pumpenwahl:
Rotationspumpe. Sie ist leise, für Festwasseranschluss geeignet, hat eine integrierte verstellbare Druckregelung.
Materialwahl Kessel/Leitungen:
Beim Material habe ich es mir nicht so leicht gemacht. Kupfer / Rotguss / Messing ist bei den Leitungen, Verschraubungen mit Sicherheit die am günstigsten und verfügbarste Wahl. Und wenn man die Ersatzteil-Kessel anderer Hersteller nimmt kommt man auch schnell zu einem Ergebniss. Die Haltbarkeit von Kupfer steht auch ausser Frage. Die Geschmacksneutralität, vor allem wenn die Maschine mal länger nicht benutzt wurde, wird da schon eher diskutiert. Für mich als Kesselselbstbauer war Kupfer wg. der Verfügbarkeit von Kupferrohr in den Dimensionen und der Mindestabnahmemenge ausgefallen. Das ideale Material wäre sowieso Glas (geschmacksneutral, korrosionsbeständig, hitzebeständig) aber die Verarbeitung und der Preis 😉
Also blieb nur noch Edelstahl. Geschmacksneutral, gut schweißbar, gut verfügbar, mittelmäßig zu verarbeiten. Wer jetzt glaubt, dass Edelstahl das Allheilmittel ist und nur ab und an eine Entkalkung braucht ist schief gewickelt. Edelstahl ist nicht Edelstahl und Edelstahl kann rosten, besser gesagt korrodieren. Also ohne das braune Zeug. Verantwortlich dafür sind die Chloridionen im Trinkwasser. Der Lochfraß wird zudem mit steigender Temperatur beschleunigt. Lang lebe der Dampfkessel.
Dem wird entgegengetreten durch:
– den „richtigen“ Edelstahl (Titanverstärkt) mit den Wundergewürzen der jeweiligen Hersteller
– der richtigen Verarbeitung (beim Schweißen unter Schutzgas muß bei Rohren und Kesseln invertiert werden, also Schutzgasatmosphäre auch von innen)
– die richtige Nachbearbeitung (beizen zur Reinigung und anschließendes Passivieren der Oberfläche, vergleichbar mit dem Eloxieren von Aluminium)
Hier die Kessel.
Die vielen Anschlußmöglichkeiten waren der späteren Flexibilität geschuldet. Davon würden aus heutiger Sicht natürlich 2/3 wegfallen.
Das Gehäuse:
Aluminiumrahmen weil:
– Kostenminimierung, ich hatte die Profile noch von einem anderen Projekt
– Lässt sich einfach bearbeiten aber schwerer schweißen
– Für nachträgliche Änderungen war der geschraubte Rahmen super, durch die vielen Schraubverbindungen aber sehr Zeitintensiv
– Ansonsten ist Edelstahl natürlich das Material der ersten Wahl
Kupferblech weil:
– Kostenminimierung, ich hatte die Bleche noch von einem anderen Projekt
– Einfache Bearbeitung (Edelstahl zu zerspanen ist eine echte Qual)
– Ich mag den Farbton und die Veränderung beim Altern. Außerdem ist der Rest meiner Küche recht „kühl“ mit viel Edelstahl/Glas/schwarzem Granit und weißen Wänden
Holz weil:
– Kostenminimierung, ich hatte das Holz noch von einem anderen Projekt
– Einfache Bearbeitung
– Ich mag Holz, siehe auch Kupfer
Die Auffangwanne, zumindest deren Holzgehäuse, empfinde ich vieleicht auch als etwas zuviel des Guten. Ist aber der Tatsache geschuldet, dass es nicht leicht ist eine Edelstahlwanne aus Blech ohne vernünftige Abkantbank zurechtzubiegen, geschweige das Ganze verzugsfrei zu schweissen. Und da die Maschine fertig war, musste eine schnelle Lösung her. Demnächst vielleicht…Die Auffangwanne selbst habe ich aus GFK laminiert.
Die Isolierung:
Bei beiden Maschinen wurden die Kessel mit Kaiflex, einem Armaflex-Konkurrenzprodukt isoliert. In meiner habe ich die Kessel nicht direkt umwickelt sondern eingehaust. Ich wollte die Stosskanten nicht verkleben, da ich davon ausgegangen bin noch öfters an die Kessel ranzumüssen. Das hätte dann Wiederaufschneiden bzw. evtl. Zerstören der Isolierung bedeutet. Zu kostspielig. Vielleicht kann man ja Klettverschlüsse aufkleben ?
Das Schöne an der Einhausung sind die geraden Flächen und das ich die einzelnen Trennwände einfach rausziehen und wieder reinstecken kann. 10 Minuten Arbeit.
Fortsetzung folgt…